Kann ein großes Presswerk Vinyl-LPs in wirklich guter Qualität herstellen? Sind sie ausschließlich den Big Playern der Musikindustrie vorbehalten? Und welchen Stellenwert hat die Schallplatte als Kulturgut für sie – geht es um Leidenschaft oder nur um Profit? Diese Fragen beschäftigen viele Vinyl-Fans. Grund genug für uns, eines der größten Presswerke der Welt zu besuchen und Antworten zu suchen: optimal media in Röbel!
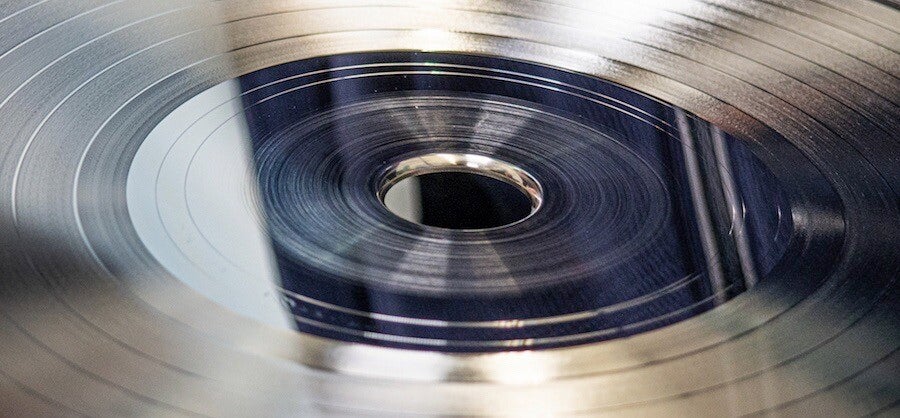
Moderne Serien-Fertigung von Schallplatten | Besuch bei optimal media
Eines vorweg: Kein Unternehmen stellt Produkte her, ohne dabei auch Gewinn erzielen zu wollen – das dürfte heutzutage jedem bewusst sein. Doch weniger offensichtlich ist die Frage, wie ein großes Unternehmen wie optimal media (im weiteren Verlauf dieses Berichts als "om" abgekürzt) es schafft, Massenproduktion, höchste Qualität und echte Vinyl-Leidenschaft zu vereinen. Wir kennen die teils unbegründeten Vorwürfe, die Presswerke weltweit im Internet immer wieder über sich ergehen lassen müssen. Gerade deshalb ist es uns wichtig, angesichts der Herausforderungen, mit denen Käufer neuer Schallplatten heute konfrontiert sind, einen genaueren Blick hinter die Kulissen zu werfen. Wir haben die Verantwortlichen mit unseren Fragen gelöchert – die spannenden Antworten findet ihr hier.
Der Blick hinter die Kulissen
Samstag, 22. April 2023: Unser Tag begann in Waren an der Müritz, wo wir von Philipp Hahn, Abteilungsleiter der Vinyl-Replikation, direkt in unserem Hotel abgeholt wurden. Unser erster Halt führte uns zu den firmeneigenen Schneidestudios, die in der historischen Villa B. untergebracht sind. Dort wurden wir bereits von Thorsten Megow, Leiter der Qualitätssicherung, und Dr. Peter Runge, Mitglied der Geschäftsleitung und Prokurist, erwartet. Vom eleganten Eingangsbereich gelangten wir schnell in einen Raum, in dem zwei beeindruckende Neumann-Schneidemaschinen standen – eine für DMM und die andere für Lackschnitte. Schneideingenieur Martin Krafft, der ebenfalls vor Ort war, erklärte uns ausführlich die Technik dieser faszinierenden Maschinen. Im stilvollen Ambiente der Villa befinden sich insgesamt noch vier weitere dieser historischen Schneidemaschinen, die uns ebenfalls in Staunen versetzten.
Schneidemaschine
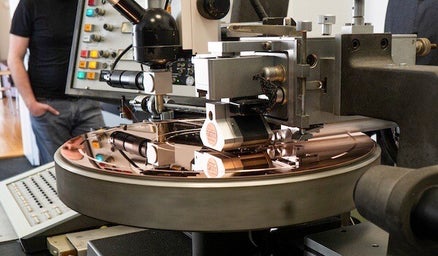
Die weltweit einzigartige Konzentration an Schneidemaschinen an einem Ort bietet gleich mehrere entscheidende Vorteile: Die komplette Produktion einer Schallplatte bleibt vollständig in einer Hand. Dadurch besteht die Möglichkeit, das gelieferte Musikmaterial von Anfang an gezielt zu bearbeiten.
Anhand von Hörbeispielen wurde uns eindrücklich erklärt, warum manche heutigen LPs so stark komprimiert klingen – und wie sich genau solche Fehler an dieser Stelle vermeiden lassen.
Ein weiterer Pluspunkt dieser eigenen Schneidemaschinen, mit denen pro Jahr etwa 15.000 Schnitte durchgeführt werden (!): Sollte während der Schallplattenproduktion ein Fehler an der Pressmatrize festgestellt werden, kann noch am selben Tag eine neue Folie oder ein frischer DMM-Schnitt angefertigt und direkt zur Galvanisierung weitergeleitet werden. Erwartungsgemäß kann dieses Audio-Mastering-Studio sowohl digitale als auch analoge Master verarbeiten – und selbstverständlich ist hier auch reines AAA möglich!
Produktionshallen
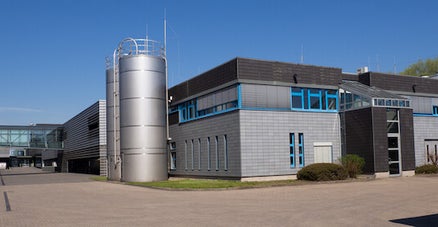
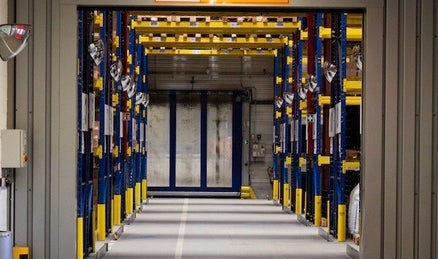
Die kurze Fahrt zum Werk gab uns bereits die Gelegenheit, die beeindruckenden Dimensionen dieser Anlage zu erfassen. Eine Vielzahl imposanter Gebäudekomplexe beherbergt die umfangreichen Produktionsstätten von om. Hier entstehen nicht nur LPs und digitale Tonträger, sondern auch Druckerzeugnisse, Buchbindungen und Medienverpackungen – alles unter einem Dach.
Als Besucher staunt man schnell über die schiere Größe, doch im Gesamtkontext macht das Konzept absolut Sinn. Om versteht sich als unabhängiger Mediendienstleister, der die gesamte Herstellungskette von Druckerzeugnissen und Datenträgern selbst abdeckt.
Im Bereich der Schallplattenproduktion bedeutet das: die vollständige Prozesskette von der Verarbeitung des Musikmaterials über die Vinyl-Herstellung bis hin zur Gestaltung und Produktion von Plattencovern, Beilagen wie Booklets und schließlich Lagerung und Versand. Im Laufe der Führung wurde deutlich, wie durchdacht das Ganze ist – sogar eine eigene Maschine zur Herstellung von Innenhüllen gehört zum Inventar.
Galvanik
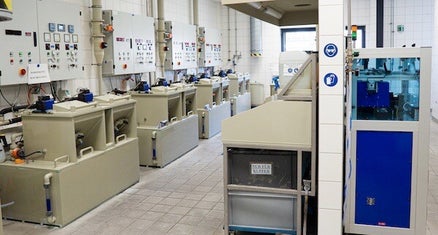
Unser Weg führte uns in die Galvanik, wo bereits der nächste Experte auf uns wartete: Bernd Altmann, stellvertretender Abteilungsleiter für Galvanik und Vinyl-Replikation.
Mit besonderer Leidenschaft erklärte er uns den Prozess, wie aus den im Schneidestudio entstandenen Matrizen durch Galvanisierung mit Silberionen der sogenannte „Vater“ entsteht. Dieser wäre theoretisch schon pressbereit und wird in einigen Fällen tatsächlich direkt verwendet – dazu später mehr. Um jedoch größere Auflagen zu ermöglichen, werden aus dem „Vater“ zunächst die „Mütter“ erstellt, aus denen wiederum die „Söhne“ gefertigt werden. Diese „Söhne“ sind es schließlich, die in die Pressmaschinen wandern und den Grundstein für die Serienfertigung legen.
DMM-Matrize
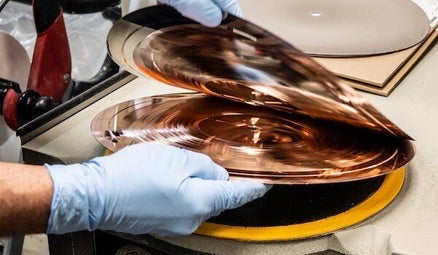
Gestanzte Pressmatrize
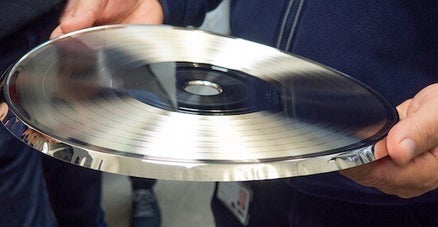
Bevor die Pressmatrizen zum Einsatz kommen, durchlaufen sie vier entscheidende Schritte, die maßgeblich zur Qualitätsverbesserung beitragen: Zunächst wird die Rückseite der Matrize poliert, um eine definierte Rauheit zu erzielen. Dieser Feinschliff sorgt dafür, dass die Matrize optimal und flach auf dem Presswerkzeug aufliegt.
Im nächsten Schritt erfolgt das sogenannte „Dehorning“ bei Matrizen, die aus Lackfolien stammen (bei DMM-Matrizen entfällt dieser Vorgang). Dabei werden kleine Unebenheiten oder „Hörner“ entfernt, die beim Schneiden am Rand der Matrize entstehen können. Ohne diesen Prozess könnten diese unerwünschten Strukturen zu Rauschen oder anderen Störgeräuschen führen.
Dieses eigens entwickelte Verfahren behebt dieses Problem zuverlässig. Anschließend wird das Mittelloch der optimierten Matrize ausgestanzt und auf perfekte Zentrierung geprüft. Stimmen die Maße exakt mit den Vorgaben überein, geht es zum nächsten Arbeitsschritt:
In einer weiteren Stanzform erhält die Matrize sowohl am Mittelloch als auch am Rand eine präzise Wulst. Diese Formgebung garantiert, dass die Matrize später unverrückbar und passgenau im Presswerkzeug sitzt. Dank dieser sorgfältigen Optimierung haben die gefürchteten Off-Center-Pressungen keine Chance – ein entscheidender Beitrag zur höchsten Qualität des Endprodukts!
Besonders in Bereichen wie der Galvanik, wo chemische Flüssigkeiten unvermeidlich sind und Verschmutzungen zu erwarten wären, fiel uns etwas Bemerkenswertes auf: alles war erstaunlich sauber. Selbst an diesem Samstag, an dem bei om die Produktion rund um die Uhr – also 24/7 – läuft, waren weder Staubansammlungen noch Schmutzecken zu entdecken. Ein Bild, das so gar nicht den häufig in einschlägigen Internetmedien verbreiteten Klischees entspricht.
Prüfplatz
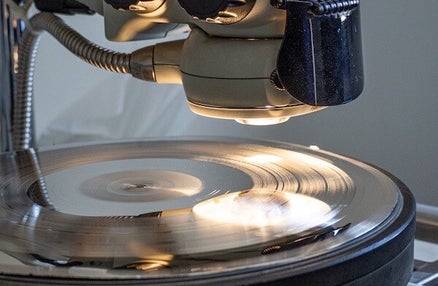
Die beeindruckende Sauberkeit begleitet uns auch in der nächsten Station unseres Rundgangs: der Halle mit über 50 Schallplattenpressen. Doch bevor wir diese betreten, werfen wir einen Blick auf den Prüfplatz. Hier unterziehen wir die LPs einer umfassenden Qualitätskontrolle. Geprüft werden unter anderem die exakte Zentrierung, die Maßhaltigkeit und natürlich die akustische Qualität. Besonders Letzteres erfordert größte Sorgfalt: Im Vier-Augen-Prinzip wird akribisch sichergestellt, dass sich keine Fehler beim Pressen eingeschlichen haben. Doch damit endet die Qualitätskontrolle noch lange nicht. Jede erste LP einer Produktion wird einer intensiven Prüfung unterzogen, und jede 400. Platte wird ins Archiv aufgenommen. Diese systematische Archivierung ermöglicht eine lückenlose Rückverfolgung und gibt uns die Möglichkeit, bei Reklamationen genau nachzuvollziehen, wann und wo ein potenzieller Fehler entstanden ist.
Halle mit Pressmaschinen
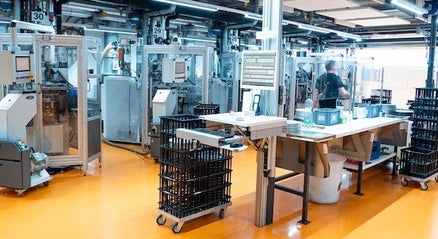
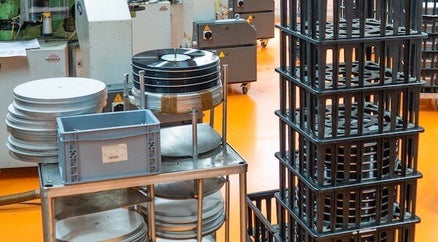
Zurück in der Fertigungshalle: Es rumpelt und pfeift aus allen Ecken – die Geräusche der zahlreichen Vinylpressen sind beeindruckend laut. Die meisten Pressen sind moderne Vollautomaten des Typs Phoenix Alpha aus Schweden, doch auch einige ältere, sorgfältig restaurierte Toolex Alpha leisten hier noch zuverlässig ihren Dienst.
Eines fiel mir sofort auf: Die frisch gepressten LPs landen zunächst auf einer Spindel. Von dort nimmt sie eine Mitarbeiterin und prüft jede einzelne LP sorgfältig auf mögliche Mängel. Erst nach ihrer Freigabe kommen die LPs auf eine neue Spindel. Nach jeweils zehn Platten wird eine Aluminium-Kühlplatte hinzugefügt, bevor die nächsten LPs gestapelt werden.
Das ist also eine zusätzliche Qualitätskontrolle! Allerdings wird bei dieser Sichtprüfung nur nach offensichtlichen Fehlern wie verrutschten Labels, Kratzern oder anderen sichtbaren Mängeln gesucht. Welligkeit der LPs wird bei diesem Prozess nicht aussortiert.
Eine kleine, aber bemerkenswerte Sache hat mir ebenfalls gefallen: Der Randabschnitt, der während des Pressvorgangs entsteht, wird direkt zu Granulat zerkleinert und dem Produktionskreislauf wieder zugeführt. Obwohl dieses Recycling nur einen kleinen Prozentsatz ausmacht, werden hier keinerlei wertvolle Ressourcen verschwendet.
Übrigens: Aus den Platten, die als Ausschuss gelten, produziert das Unternehmen neue LPs, die intern als "Re-Vinyl" bezeichnet werden. Dafür werden die Plattenlabels entfernt und das Material zu Granulat verarbeitet. Das ist jedoch nur ein Teil der umfassenden Öko-Philosophie, die dahinter steckt.
Maschine für Innenhüllen
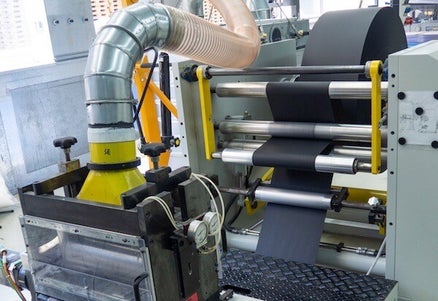
Wir betreten nun den Bereich, in dem Innenhüllen und Plattencover hergestellt werden, und erfahren mit Überraschung, dass diese Abteilung nur für unseren Besuch in Betrieb ist! Normalerweise arbeitet sie nur an Wochenenden bei erhöhtem Bedarf oder in Ausnahmefällen.
Besonders beeindruckend war die riesige Maschine zur Herstellung der Innenhüllen. Sie kann sowohl einfache Standardhüllen als auch Varianten mit Innenfolie produzieren. An dieser Stelle gab es einen interessanten Hinweis, den auch andere Presswerke häufig betonen: Sie empfehlen Auftraggebern stets, gefütterte Innenhüllen zu bestellen. Dennoch entscheiden sich viele aus Kostengründen dagegen.
Das führt dazu, dass neue LPs durch das raue Papier der Standardhüllen häufig leichte Oberflächenkratzer bekommen – ein Problem, das nicht den Presswerken angelastet werden kann.
Druckmaschinen

Plattencover-Produktion
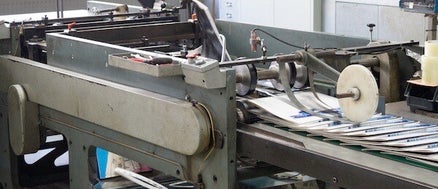
Ein häufiges Problem bei Schallplattenverpackungen sind durchstoßene Kanten bei den Covern. Om empfiehlt den Plattenlabels daher, bei Klappcovern die LPs zwischen die Taschen zu legen, um sogenannten Seam Split zu vermeiden. Dennoch zeigen sich viele Auftraggeber zurückhaltend und bevorzugen nach wie vor die traditionelle Verpackungsmethode, bei der die LPs direkt in die Taschen eingelegt werden.
Überprüfung am Mikroskop
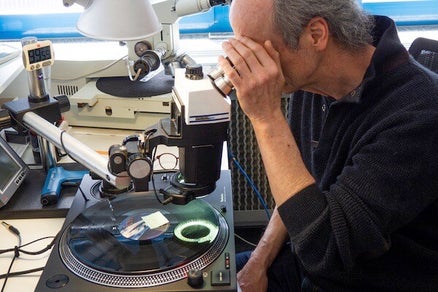
Zum Abschluss führte mich der Weg noch einmal in den Raum von Thorsten Megow, der in der Zwischenzeit zwei von mir mitgebrachte Schallplatten unter dem Mikroskop untersucht hatte.
Beide LPs zeigten entlang der Rillen hell schimmernde Punkte, die jedoch unterschiedlich stark ausgeprägt waren. Wie er mir erklärte, entstehen solche Punkte, wenn sich eine Schallplatte beim Auspressen nicht sauber von den Matrizen löst und kurzzeitig zurückfedert. In diesem Moment berührt die noch über 50°C warme Vinylplatte erneut die Pressform, wodurch diese feinen Beschädigungen in der Rille entstehen.
Diese schimmernden Stellen werden im Englischen als „Stitches“ bezeichnet, während man sie hier bei uns scherzhaft „Nähmaschine“ nennt.
Im Gespräch
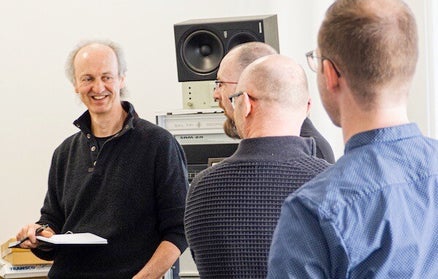
Worüber wir uns an dieser Stelle alle amüsiert haben, kennzeichnet auch etwas, das uns schon während des gesamten Besuches aufgefallen ist: diese fünf Führungspersonen von optimal media, die uns begleitet und alles erklärt haben, offenbarten alle eine erstaunliche Begeisterung für ihre Arbeit. Immer wieder blitzte die Begeisterung für das Thema der Schallplatte auf, mit viel Engagement haben sie uns mit fachlichen Details fast schon überschüttet.
Es war also alles andere als eine gelangweilte Führung, die sie „durchziehen mussten“ - genau das Gegenteil war der Fall: jeder hat mit sichtbarer Freude über seinen Fachbereich erzählt. Das Ganze hat schon alleine aus diesem Grunde Spaß gemacht und was ich auch klasse fand: alle meine kritischen Fragen und teils gar provokativen Hinweise auf die Probleme der Vinyl-Fans, die sich mit Fehlpressungen herumschlagen müssen, haben sie gelassen und mit viel Kompetenz beantwortet!
Abschließend noch ein kleiner Hinweis: Es wird oft behauptet, dass Unternehmen wie optimal media ausschließlich für Major Companies produzieren. Das entspricht nicht der Wahrheit!
Etwa ein Viertel der täglich produzierten 750.000 bis 800.000 LPs, Singles und Maxi-Singles wird an Indie-Labels geliefert. Der kulturelle Wert der Schallplatte spielt bei optimal media also weiterhin eine bedeutende Rolle. Auch om-Geschäftsführer Jörg Hahn sieht diesen Aspekt bei den Majors noch nicht vollständig verloren. Die Hoffnung bleibt – und das ist ein gutes Gefühl!
Erstelle deine eigene Website mit Webador